Understanding LOLER: requirements, inspection checklists and meaning
Discover everything you need to know about LOLER requirements, including its meaning and inspection checklist. Learn how to comply with LOLER regulations and ensure safety in lifting operations.

Mark Andrew
Health & Safety Consultant Mark is an experienced Health & Safety advisor with a strong background in engineering. He holds an MEng and BEng (Hons) in Engineering, is a Practitioner of IEMA, and a Graduate Member of IOSH.Date
06 August 2024Updated
06 August 2024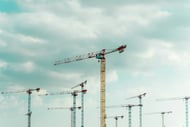
Table of contents
Related articles
Tags
Understanding LOLER: The three main principles
The acronym LOLER stands for The Lifting Operations and Lifting Equipment Regulations 1998. LOLER requirements are enforced by the UK Health & Safety Executive (HSE). These principles are part of broader legislation known as the Health and Safety at Work etc. Act 1974.
When it comes to the meaning of LOLER, the main principles of the regulations are as follows:
- To guarantee the safety of all lifting activities.
- To set requirements for the safe use of lifting equipment.
- To establish guidelines for thorough inspections of lifting equipment at appropriate intervals by a qualified person with the knowledge and skills to do so.
What does LOLER mean and cover?
Lifting operations will always carry a high level of risk, so it's important that such operations are made as safe as possible.
Some of the risks associated with lifting include:
- Overloading (lifting more weight than the equipment's maximum capacity)
- Poor load security (loads not properly secured can shift or fall, posing a serious danger to workers and bystanders)
- Equipment failure
- Lack of proper training
- Lifting on unstable ground/surfaces
- Weather conditions (strong winds can affect equipment stability)
- Obstructions
- Limited visibility
- Poor communication and human error
- Mechanical shock
LOLER are rules designed to eliminate the risks above, and to make lifting as safe as possible. The requirements ensure the use of strong, stable equipment, safe positioning, conducting regular checks and frequent maintenance. As well as proper equipment storage to extend its lifespan.
LOLER also requires careful planning for each lift, considering all potential risks, and keeping relevant safety records (such as inspection reports and safe working load details). Those managing lifting operations must also ensure that operators are properly trained and experienced.
LOLER specifically applies to lifting equipment used only for work purposes. For example, a goods lift in a store is covered, but a customer lift is not. Escalators have separate regulations, and items like dentist chairs are considered low-risk, so are not covered by LOLER.
That said, even if equipment isn't covered by LOLER, it's still likely covered by the Provision and Use of Work Equipment Regulations (PUWER), which enforces similar rules for inspection, maintenance and training. A good example of this is a pallet truck. Manual hand pallet trucks lifting to heights of 300mm or less now remain under PUWER, while those lifting above that height would be considered under LOLER.
In any event, the HSE has confirmed that it is always for the duty holder and competent person to carry out a risk assessment of work equipment to determine whether it should be examined in accordance with LOLER or PUWER.
The Health and Safety at Work Act also requires employers and the self-employed to ensure the safety of anyone affected by their work, including employees, customers and the general public. It's important to remember that even if LOLER doesn't apply, other safety laws will.
LOLER inspection frequency: 6 or 12 months?
Choosing the right frequency for LOLER examinations is really important to maintain safety and comply with legal requirements. While the regulations provide minimum inspection intervals, these should be adjusted based on how often the equipment is used and the environment it operates in. For instance, equipment that has frequent use, or comes into contact with challenging conditions will be inspected more often.
New equipment requires a thorough examination before its first use, unless it has a valid declaration of conformity less than 12 months old. Equipment used for lifting people should be inspected at least every 6 months, while other lifting equipment should be checked at least annually. In high-risk situations, such as exposure to corrosive environments or extreme use, more frequent inspections by a competent person may be needed.
Understanding the LOLER standard: key points
The LOLER standard focuses on setting clear requirements for lifting equipment and practices. Key aspects include selecting lifting equipment that is strong and stable, conducting thorough inspections before the equipment is used for the first time, and performing regular checks.
Alongside inspections, proper record-keeping and maintenance, as well as load details, are also considered essential to demonstrate compliance and to track the equipment’s condition.
LOLER also requires that lifting operations are carefully planned, considering all potential risks to prevent accidents. Only trained and competent personnel should operate lifting equipment to ensure safe practices are followed.
What equipment needs to be LOLER tested?
LOLER regulations apply to a range of lifting equipment, including car lifts used in repair garages, cranes for construction and their support runways, goods and passenger lifts, hoists for patients in hospitals and care, lorry lifts for loading and unloading heavy goods, telescopic handlers used in agriculture, and vehicle cranes for heavy construction work.
As well as lifting equipment, LOLER also covers lifting accessories such as eyebolts, hooks, ropes, slings and spreader beams. These accessories are vital for safe lifting operations.
What does LOLER not cover?
Some equipment is not covered by LOLER, such as roller shutter doors, escalators, tipper trucks and fall arrest systems. Although these items aren't subject to LOLER, they fall under other regulations like the Provision and Use of Work Equipment Regulations 1998 (PUWER).
Does LOLER apply to unassisted lifting?
LOLER applies only to lifting equipment used at work. Some equipment that moves people or goods continuously, like escalators or travelators, and some conveyor belt systems, aren't covered by LOLER.
This equipment is however subject to the Provision and Use of Work Equipment Regulations (PUWER), which covers aspects such as selection, inspection, maintenance and training. Pallet trucks that only lift loads slightly off the ground also don't fall under LOLER regulations, but come under PUWER.
Do ladders fall under LOLER requirements?
Any ladder used at work is considered work equipment and falls under the Provision and Use of Work Equipment Regulations 1998 (PUWER). This legislation requires suppliers and users to ensure that work machinery, including ladders, is provided and used safely.
What are the consequences of not following LOLER regulations?
Failing to comply with LOLER regulations carries significant risks, including increased chances of serious injury or even death.
When lifting equipment isn't regularly inspected and maintained, it can malfunction or fail, potentially hurting those operating it, or bystanders. This not only endangers lives, but also carries many legal risks, including fines, premises closures and prosecution for non-compliance.
Regular LOLER inspections are crucial for maintaining the safety and integrity of lifting equipment. These inspections identify wear and tear, faults, or defects that could compromise equipment performance.
By following a comprehensive LOLER inspection checklist, businesses can prevent accidents and safeguard their employees' well-being. Adhering to the LOLER inspection checklist helps companies avoid severe legal consequences, such as penalties from the Health and Safety Executive (HSE).
Stay compliant with LOLER requirements
Our experienced, highly qualified health and safety consultants at Neathouse Partners can advise on LOLER regulations and answer any questions you may have.
Contact us on 0333 041 1094, or book in a call with one of our team.
Related blog posts
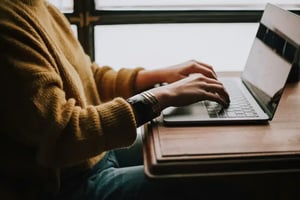
Employees' rights at work during cold weather
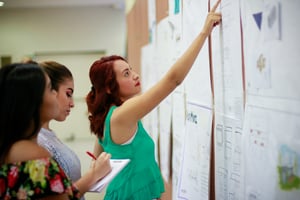
Ensuring Compliance with Displaying the Health and Safety Law Poster
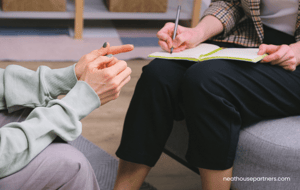
Drinking alcohol at work: an employer's guide to alcohol policy
Have questions?
Get in touch today
Contact us, and our team will get back to you within 24 hours. We value your questions and are committed to getting them answered quickly.
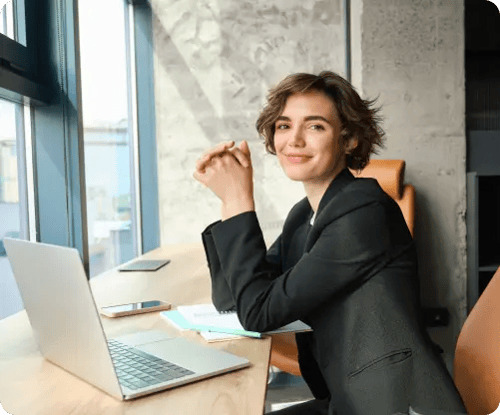
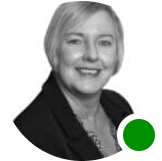
Hello! I am Nicky
Just fill in the form below with your details, and I will arrange for a member of our team to give you a call.
By clicking, you agree to our Privacy Policy